alwepo.com, Plastic Extrusion Products – Plastic extrusion, a versatile manufacturing process, involves the forcing of melted plastic through a die to create shapes with fixed cross-sections. Widely utilized in both industrial and domestic applications, plastic extrusion enables the efficient production of a myriad of shapes, contributing to the creation of essential products across various sectors. This article explores products made with plastic extrusion, explaining their various uses and importance in today’s society.
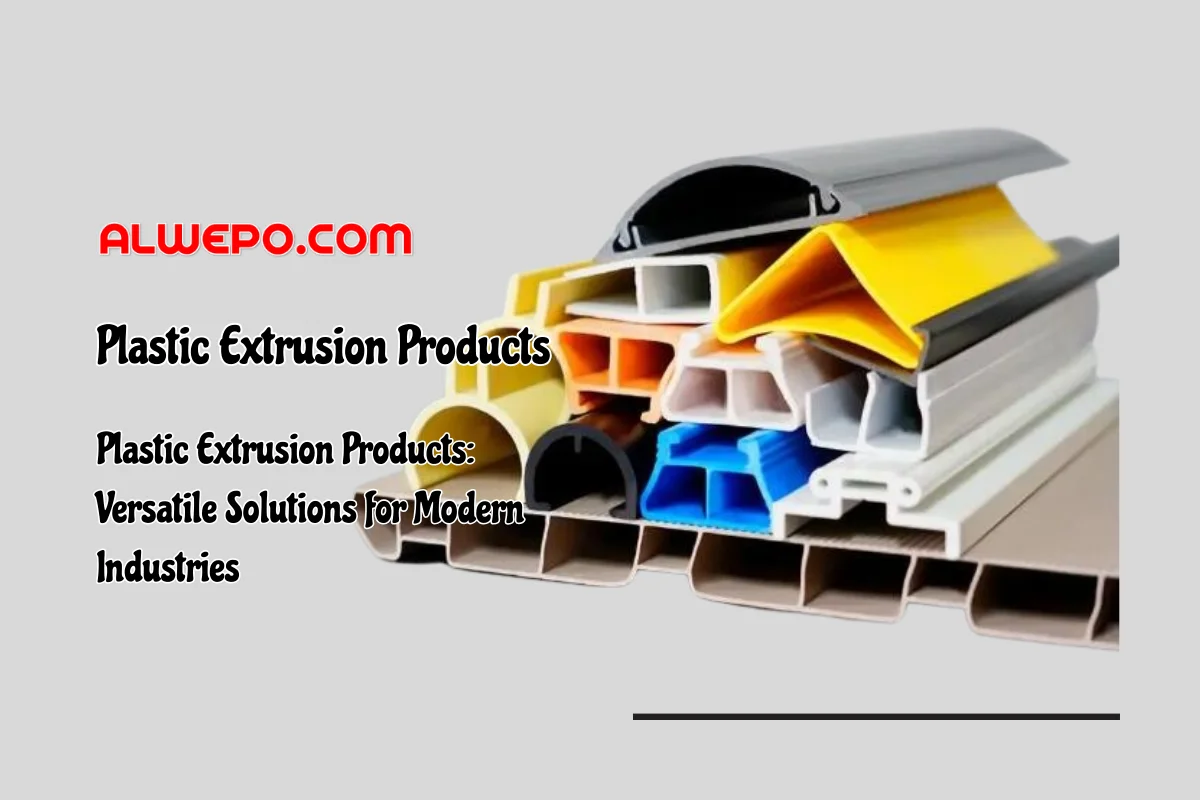
Hollow Pipe and Tubing: Essential Conduits for Fluid Transportation
Plastic extrusion plays a pivotal role in the production of hollow pipes and tubing, which serve as indispensable conduits for transporting fluids and gases in numerous applications. Polyvinyl chloride (PVC) pipes, commonly used for water and sewer systems, exemplify the versatility of plastic extrusion in creating large-scale conduits for industrial and municipal use. These pipes, with diameters ranging from standard sizes to several feet, facilitate the efficient conveyance of liquids and sewage.
In addition to PVC pipes, plastic extrusion produces micro-miniature medical tubes used in critical healthcare settings, where precision and reliability are paramount. These tubes, with diameters as minuscule as 0.010 inches, play a crucial role in delivering oxygen in intensive care units, fuel in small engines, and beverages through drinking straws. The versatility of plastic extrusion in creating hollow conduits underscores its significance in meeting diverse industrial and medical needs.
Solid Shapes: Versatile Raw Materials for Industrial Applications
Plastic extrusion also yields solid shapes, including round, square, and hexagonal bar stock, as well as rectangular pieces, which serve as essential raw materials in various industrial processes. These standardized thermoplastic shapes offer versatility and flexibility, catering to the specific requirements of machine shops and manufacturing facilities. From automotive components to consumer electronics, solid plastic shapes find application across diverse industries, contributing to the efficient production of high-quality products.
Moreover, extruded decking, planks, and structural pieces have gained popularity in recent years as sustainable alternatives to traditional building materials. Made from recycled plastics, these extruded plastic products offer durability, weather resistance, and low maintenance, making them ideal for outdoor furniture, fencing, and park benches. The widespread adoption of extruded plastic lumber underscores its potential to revolutionize the construction industry and promote sustainable building practices.
Sheeting and Film: Functional Materials for Various Applications
Plastic extrusion enables the production of sheeting and film materials used in a wide range of applications, from glazing and packaging to protective barriers and machine components. Polycarbonate sheeting, known for its impact resistance and durability, finds application in window glazing, machine guards, and automotive components, providing robust protection against environmental hazards and physical impacts.
Similarly, acrylic plastics are extruded into thin sheets for glass replacements, offering clarity, weather resistance, and versatility in design. Clear plastic films produced through extrusion serve diverse purposes, including short-term food packaging, retail packaging, and protective covers. Blister packs, a type of extruded hard film softened by heat and molded into shape, are commonly used in pharmaceutical packaging, ensuring product integrity and safety.
Profile Shapes: Customized Solutions for Specific Needs
Extrusion is widely employed in the production of profile shapes, which serve as customized solutions for a myriad of applications, ranging from automotive components to architectural elements. Windshield wiper blades, squeegees, rain gutters, and automotive trim are examples of extruded shapes used in various industries, offering durability, weather resistance, and aesthetic appeal.
Vinyl siding, a popular choice in residential construction, is manufactured through plastic extrusion, offering homeowners a low-maintenance and weather-resistant cladding solution. With its wide array of colors, textures, and profiles, vinyl siding enhances the curb appeal and durability of homes, contributing to sustainable and aesthetically pleasing architectural designs.
Extruded Blow Molded Items: Versatile Containers and Packaging Solutions
Plastic extrusion facilitates the production of blow molded items, including bottles, jars, and containers, which serve as versatile packaging solutions for various industries. The blow molding process involves extruding a hollow tube of plastic, known as a parison, and inflating it to the desired shape using compressed air. This method enables the efficient production of containers in diverse shapes and sizes, catering to the specific requirements of food and beverage, pharmaceutical, and consumer goods industries.
Insulated Wire: Essential Components for Electrical and Industrial Applications
Plastic extrusion plays a crucial role in the production of insulated wire, providing electrical conductivity, insulation, and protection against environmental factors. In this process, the wire is passed through a die, where the insulation material is extruded around it, ensuring optimal performance and safety in electrical applications. Additionally, non-electrical cables are coated through plastic extrusion to enhance corrosion resistance, abrasion resistance, and handling capabilities, making them ideal for industrial and marine applications.
Conclusion
The diverse array of products created using plastic extrusion underscores its significance in modern manufacturing and construction industries. From conduits and structural components to packaging materials and electrical insulation, plastic extrusion enables the efficient production of essential products across various sectors. As industries continue to prioritize innovation and sustainability, plastic extrusion remains a cornerstone of modern manufacturing practices, offering versatile solutions to meet evolving needs and challenges. With ongoing advancements in materials, technologies, and processes, the future of plastic extrusion holds tremendous promise for creating a more sustainable and resilient built environment.