alwepo.com, Die Casting Mold Design – Die casting stands as a quintessential technique for mass-producing metal products and components. At the heart of this intricate process lies die casting mold design – a critical step that dictates the shape, quality, and uniformity of the final product. With precision and meticulous attention to detail, engineers craft molds tailored to exact specifications, ensuring seamless production and superior outcomes.
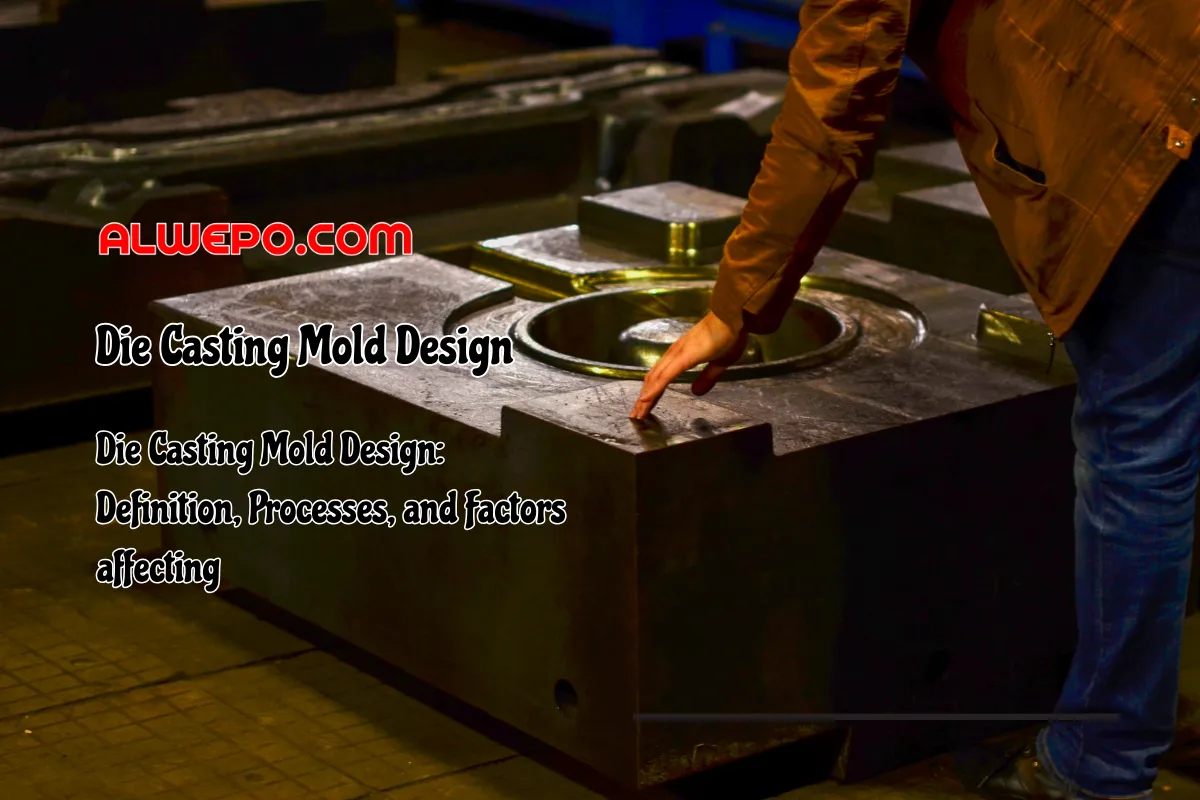
In this comprehensive guide, we delve into the nuances of die casting mold design, exploring the key factors, considerations, and techniques that underpin this essential aspect of manufacturing excellence.
What Is Die Casting Mold Design?
Die casting mold design is a critical aspect of the manufacturing process, essential for producing high-quality metal products efficiently and effectively. In essence, it involves creating precise and intricate molds that determine the shape, features, and characteristics of the final casted parts.
This meticulous process requires careful consideration of various factors such as geometry, material properties, and production requirements to ensure optimal performance and consistency in the finished products. By mastering the art of mold design, manufacturers can achieve superior results, streamline production processes, and meet the demands of diverse industries with precision and excellence.
Die Casting Mold Design Process
Die casting is a high-pressure casting process that produces complex metal parts with high precision and repeatability. The success of the die casting process hinges on the meticulous design and creation of the mold. This guide delves into the intricacies of the die casting mold design process, outlining each crucial step involved in crafting a mold that delivers exceptional results.
Step 1: Analyze 2D/3D Drawings
The journey begins with a thorough examination of the 2D or 3D drawings of the part to be cast. This analysis focuses on understanding the part’s geometry, dimensions, tolerances, and any specific features or requirements. The designer meticulously reviews these details to ensure the mold can accurately replicate the desired part.
Step 2: Determine Injection Type
This step involves selecting the most suitable injection type for the casting process. Factors like the desired plasticization rate (the rate at which the molten metal is melted and converted into a moldable state), the volume of metal required per casting, and the complexity of the part all influence this decision. Common injection types include hot chamber die casting and cold chamber die casting, each with distinct advantages and limitations.
Step 3: Determine Cavities
The number of cavities, or the number of identical parts produced in a single casting cycle, is determined in this step. Considerations include the product geometry, the required production volume, dimensional accuracy needs, and economic factors. For high-volume production runs, multiple cavities can increase efficiency, while single-cavity molds may be more suitable for complex parts or low-volume production.
Step 4: Determine Parting Surface
The parting surface, also known as the split line, defines how the mold will open and close to allow for part removal. The designer prioritizes both ease of mold operation and efficient part formation when selecting the parting surface. Ideally, the parting surface should minimize the need for complex mold components and ensure smooth separation of the mold halves after casting.
Step 5: Design Gating System
The gating system plays a critical role in delivering molten metal into the mold cavity. This step involves designing the gate location, which determines the entry point of the molten metal into the cavity, and selecting the runner system, which is the network of channels that carries the molten metal from the sprue (the initial entry point) to the gate. A well-designed gating system ensures proper filling of the cavity, minimizes turbulence and air entrapment, and facilitates solidification.
Step 6: Design Ejector System
The ejector system is responsible for efficiently removing the solidified casting from the mold cavity after solidification. This step involves designing the ejector pins, their placement within the mold, and the actuation mechanism that will safely and effectively push the casting out. A well-designed ejector system minimizes the risk of part damage during ejection and contributes to a smooth production cycle.
Step 7: Design Cooling System
The cooling system is vital for controlling the solidification rate of the molten metal within the mold cavity. A uniform and efficient cooling system ensures consistent part quality and dimensional accuracy. This step involves designing the placement and configuration of cooling channels within the mold to achieve optimal heat transfer from the solidifying metal to the cooling system. The impact of the cooling system on the mold structure and its potential for creating stress concentrations is also carefully considered.
Step 8: Determine Guide Device
Guide devices, often referred to as guide pins and bushings, ensure precise alignment of the mold halves during opening and closing. The selection of the guide device type (sleeve guides, dowel pins, etc.) is based on the mold base type (the standardized base plate on which the mold components are mounted) and the required level of precision for part alignment.
Step 9: Select Mold Steel
The choice of mold steel is crucial for ensuring the mold’s durability and resistance to the high temperatures and pressures encountered during the die casting process. Factors like the expected casting batch size, the type of metal being cast, and the desired casting quality all influence the selection of the most appropriate steel grade.
Step 10: Draw Assembly Drawing
The assembly drawing serves as a blueprint for the complete mold. It depicts how the various components – pouring system, cooling system, ejector system, and mold halves – come together to function as a cohesive unit. This drawing ensures all components are properly coordinated and function seamlessly during the casting process.
Step 11: Draw Main Mold Parts
Detailed drawings of the individual mold components, such as the mold halves, core inserts (used to create internal features), and cavity inserts (which define the part shape), are created in this step. These drawings specify all critical dimensions, tolerances, and surface finishes required for accurate manufacturing of the mold components. Manufacturability is a key consideration here, ensuring the design is optimized for efficient and cost-effective mold production. This involves:
- Standardization: Utilizing standardized components whenever possible, such as commercially available mold bases and guide devices, can significantly reduce design time and manufacturing costs.
- Machinability: The design should consider the machining capabilities and limitations of the equipment used to create the mold components. Complex geometries or tight tolerances that are difficult or expensive to machine should be avoided if possible, or alternative manufacturing methods such as additive manufacturing may be explored.
- Parting Lines: The location of parting lines on the mold halves should be strategically placed to minimize the need for complex machining operations or additional mold components. This helps to streamline the manufacturing process and maintain cost-effectiveness.
- Mold Release: The drawings should specify the use of appropriate mold release agents to facilitate the separation of the mold halves after casting and prevent sticking of the cast part. The chosen release agent should be compatible with the mold material and the casting metal.
- Surface Finish: The surface finish requirements for each mold component should be clearly defined in the drawings. Different areas of the mold may require varying degrees of smoothness or texture, depending on the desired surface finish of the cast part. Balancing the need for a high-quality surface finish with the practicalities of machining is crucial.
- Assembly Considerations: The design should account for the ease of assembly and disassembly of the various mold components. This includes ensuring proper clearances for components to fit together smoothly and incorporating features that facilitate alignment and fastening during mold assembly.
Step 12: Implement Exhaust System
A well-designed exhaust system is essential for achieving high-quality castings. Entrapment of air within the mold cavity can lead to surface defects and incomplete filling. This step involves incorporating exhaust slots or inserts within the mold to facilitate the evacuation of air during the casting process. The placement and size of these exhaust features are critical for effective air removal without compromising the integrity of the mold or the cast part.
Additional Considerations:
-
Draft Angle: Die casting molds often incorporate a slight draft angle on the sidewalls of the cavity. This draft angle allows for easier removal of the solidified casting from the mold and reduces the risk of tearing or damage.
-
Surface Texture: The desired surface finish of the cast part influences the surface texture of the mold cavity. A smooth mold surface will generally produce a smooth cast part, while a textured mold surface can be used to create specific surface features on the casting.
-
Safety Features: Die casting is a high-pressure process, and safety is paramount. The mold design should incorporate features to minimize the risk of injury during operation, such as proper venting for steam and interlocks to prevent accidental mold closure while the machine is running.
-
Simulation Software: Modern die casting mold design often utilizes computer-aided design (CAD) software and simulation tools. These tools allow designers to virtually model the casting process, analyze potential issues like stress concentrations or uneven cooling, and refine the mold design before physical mold creation begins.
The Crucial Role of Die Casting Mold Design
Die casting molds serve as the cornerstone of the entire die casting process, exerting a profound influence on the outcome of each manufactured part. A well-designed mold is not merely a vessel for molten metal; it is a meticulously engineered instrument that shapes and defines the very essence of the final product. From intricate geometries to precise configurations, every aspect of the mold design plays a pivotal role in determining the quality, efficiency, and cost-effectiveness of the manufacturing process.
Importance of Effective Mold Design Factors
A myriad of factors come into play when designing a die casting mold, each contributing to the overall quality and performance of the final product. Here are some key considerations that shape the mold design process:
1. Draft
Draft refers to the taper applied to the mold core, facilitating the smooth ejection of the casting from the die. The degree of draft varies based on factors such as the type of alloy used, wall geometry, and mold depth. Proper draft angles are essential to prevent sticking and ensure uniform part release.
2. Fillets
Fillets are concave junctions that smooth angled surfaces and prevent sharp corners, which can impede the casting process. By incorporating fillets into the mold design, engineers mitigate the risk of production errors and enhance the overall quality of the finished product.
3. Parting Lines
The parting line, or parting surface, delineates the boundary between different sections of the mold. Precise positioning of the parting line is crucial to prevent material leakage and ensure uniform molding. Any deviation or deformation of the parting line can lead to defects and inconsistencies in the final product.
4. Bosses
Bosses are protruding features in the mold that serve as mounting points or stand-offs. To maintain uniform wall thickness in the molded product, engineers often incorporate holes into the interior structure of the bosses. Careful consideration of boss design is essential to optimize material flow and prevent casting defects.
5. Ribs
Ribs are structural elements added to improve material strength and rigidity in areas with insufficient wall thickness. Strategic placement of ribs can minimize stress cracking, enhance product durability, and optimize fill capabilities. By reinforcing critical sections of the mold, engineers ensure the integrity and performance of the final product.
6. Holes and Windows
Incorporating holes and windows into the mold design facilitates the ejection of completed moldings and enables the creation of substantial drafts. Additional features such as overflows and flashovers may be necessary to control material flow and prevent casting defects. By carefully managing the placement and geometry of holes, engineers optimize the production process and ensure consistent part quality.
7. Symbols
Brand names or product logos are often included in the mold design to enhance brand recognition and aesthetics. While symbols themselves do not complicate the casting process, their incorporation can impact production costs and material usage. Engineers must carefully evaluate the design and placement of symbols to minimize waste and optimize efficiency.
Achieving Excellence in Die Casting Mold Design
In the realm of die casting mold design, precision, innovation, and attention to detail are paramount. By leveraging advanced technologies, computational tools, and industry best practices, engineers can optimize mold performance, streamline production processes, and deliver exceptional results. From concept development to final validation, each stage of the mold design process requires meticulous planning, analysis, and refinement to ensure superior outcomes and maximize manufacturing efficiency.
Conclusion
Die casting mold design represents the nexus of art and science – a harmonious blend of creativity, ingenuity, and technical expertise. From intricate geometries to complex configurations, each mold is a testament to the craftsmanship and innovation of its creators. By embracing the principles of effective design and continuous improvement, engineers can unlock new possibilities, push the boundaries of innovation, and redefine the future of manufacturing excellence. As the backbone of the die casting process, mold design serves as a testament to human ingenuity, shaping the world around us one precision-crafted part at a time.